the Fellowship of the Holland Onion - part 6
In the sixth installment of our video series, ‘The Fellowship of the Holland Onion,’ we join fellow companion and onion packer Remko Wilms as he processes the final batch of Holland Onions from renowned grower Co van den Dries. Carefully tailed and sorted, the onions lie in wait in the bunker, ready for the next leg of their journey. Soon, they’ll be automatically bagged in durable woven net packaging, each 25-kilogram bag designed for efficiency and stability. Once palletized into secure patterns, these onions will embark on their voyage to export destinations around the world.
The Dutch onion chain can realise every packaging wish quickly and efficiently. Paper, net or foil packaging, crates, trays, cardboard boxes or bins are all possible. Within 48 hours, the Holland Onion can be on its way to its final destination.
Packaging plays a unique role in the life journey of the Holland Onion. To start with, there is the choice of primary packaging material. For the ever-decreasing packaging quantities for the Dutch and European domestic market, this is tubular netting. This allows both one individual onion up to 2.5 kilograms of Holland Onions to be automatically packaged, in all colours of the rainbow. This can be done as a loose net, as clip-to-clip or as a carry bag. When closing retail packaging, these are provided with strip tags, swing tags, dangler tags, printed wine glass labels or any other labels. These are usually provided with the supplier, grower, Global Gap number (GGN), parcel number, country of origin, class and size.
Export market
For the export market, automatic packaging in wicketed, woven net packaging is almost always chosen. These net packaging are light, graceful and extremely strong and are available in bag sizes of 2.5, 5, 10, 18, 22.5, 25 and 30 kg
What is wicketed net packaging?
Wicketed net packaging are actually bundled bales of net packaging. These always have a laminated top with two perforated holes, which fit exactly on the wicket of the machine. The laminated top is necessary to enable the automatic onion packaging process.
A complete bale with wicket net packaging usually consists of 1000 bags. The exact required packaging quantity for an export batch of Holland Onions is manually positioned by the operator on the pins in the supply carousel of the packaging line. The net packaging is then sucked in with suction cups to be opened individually and filled with onions fully automatically.
Monomaterial
Net packaging consists entirely of recyclable polypropylene and can be manufactured with or without bottom fold or side folds. Ten-colour printing of a private label takes place on the available surface in the middle and is based on water-based inks. Closure can be carried out with permanent or resealable tape. At the destination, the net packaging is often reused locally many times before it can finally be recycled as reusable raw material for new applications.
Stable export pallets
The automated palletising process then takes place. The dimensionally stable net packagings with Holland Onions are stacked in a horizontal position on a pallet according to thought-through pallet stacking patterns. On the pallet outfeed conveyor, the pallet load is then wrapped once more with a tightly spun strapping net for extra stability during overseas transport. If desired, the bales can be delivered on disinfected pallets.
Holland Onions can also be palletised in their primary net packaging in cardboard octabins (250 kg). Or they can be filled loose in well-ventilated FIBCs (big bags) of up to 1,500 kilograms. Final packaging then takes place in the export country itself.
Artificial Intelligence and the Holland Onion
From the trusted hands of Remko, we also make a quick switch to the latest companion of the Holland Onion: Artificial Intelligence. AI is already fully involved in the future of the onion industry.
99.9% flawless onions
With the help of AI, each side of the Holland Onion is photographed from all sides before the packaging process and scanned internally using infrared technology. Every onion that ends up in its export packaging is therefore 99.9% certain to be absolutely flawless, both inside and out.
Knowledge transfer to AI
In order to achieve this accuracy, AI has been taught to assess the quality of the Holland Onion based on 170,000 different images in 17 categories. This means that the customer can be served exactly according to his wishes.
No waste
Deviating onions are automatically sorted out in the buffer zone and are immediately given a different destination, because no onion is wasted. For example, onions with a deep cut go to a factory where they are diced and onions that are too soft go to the oil press, so that natural flavour components such as onion oil can be made from them. The pulp of onions can be valorised as animal feed. Even the outer dry layers that are released during the process are used, either for fermentation to produce biogas. Or even more valuable as a raw material for natural colourings.ut the Dutch onion chain is also anticipating the trend of ever-smaller households. It is creating efficiently stackable cardboard display packaging for this purpose, which can be direclty placed on the shelves of European supermarkets.
Or to a very customized request to deliver only three, but then really perfect looking and completely identical Holland Onions, in a tightly fitting small tube package.
Nothing is too crazy for the Holland Onion Association. Just toss us an onion!
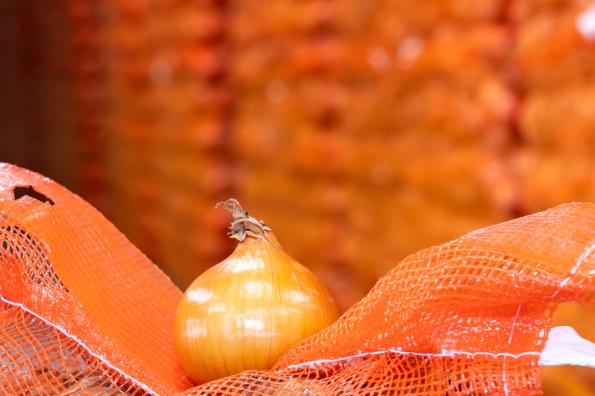