why onions travel in nets
Did you know onions remain active at a cellular level until the moment they’re consumed? Even after being harvested from the soil, Holland Onions continue their metabolic activities—breathing, exchanging moisture, and maintaining their vitality. This living nature makes packaging more than just a protective layer; it’s a crucial tool for preserving quality and regulating the onion's delicate physiological processes.
Woven net packaging plays an important role in maintaining the peak quality of Holland Onions and has a direct influence on how the physiology of the onion is supported.
Good air circulation and respiration
Onions continue to absorb oxygen and emit carbon dioxide during transport. Although this respiration process is minimal, it generates heat and moisture. Net packaging ensures free air circulation around the onions, which allows the removal of this heat and moisture. This prevents condensation, which is beneficial to prevent mold growth and rot.
Heat dissipation
During respiration, onions generate heat. A closed package can retain this heat, which leads to an acceleration of biological processes, including premature sprouting. Net packaging minimizes this risk.
Controlling moisture loss
Onions lose moisture through transpiration. In a closed environment, this can lead to condensation, which is harmful to the onion. Good ventilation is essential, especially when temperature differences occur during transport. Because no moisture can accumulate, Holland Onions have a better shelf life in their net packaging and retain their firm skin, structure and crispness.
Packaging and transport
Woven net packaging therefore offers both sufficient flexibility and strength to protect the onions during transport, without sealing them off from their environment. At 40 grams, net packaging is also feather-light, which increases logistical efficiency and keeps the environmental impact and transport price low. In a standard packaging of 25 kilos of Dutch onions, the packaging only makes up 0.15 percent of the total weight, which is unique!
Jute onion bags
Jute bags
Once upon a time, Dutch onions embarked on their journeys packed snugly in rough, sturdy jute bags. These iconic sacks, with their coarse texture and earthy aroma, were a staple of the onion trade. But in the 1950s, everything changed. A revolutionary invention—the woven net bag—quickly replaced the humble jute. Unlike jute bags, which often conformed to the whims of their contents, net bags offered structure, stability, and superior functionality, marking the beginning of a new era in onion packaging.
The predecessor of the current net packaging around 1950, the woven paper bag. (by courtesy of the Royal NNZ Group)
The first net packaging was created in America shortly after the Second World War and was woven from paper. With the introduction of synthetic materials in the 1970s, the paper on the weaving machines was gradually replaced.
Downgauging
Since the introduction of synthetic net packaging, the industry has succeeded in making it increasingly lighter and more efficient. Innovative research has made it possible to create increasingly efficient blends of raw materials, which make downgauging possible. This means that an increasingly thinner film has been produced with the same strength and other required properties. This saving on raw materials makes a less intensive - and therefore more sustainable - extraction process possible. Since the introduction of synthetic net packaging, it has now become three times lighter than its paper predecessor.
small weight for large quantities
With only 40 grams of extremely thin woven material, the current net packaging can contain large quantities of onions (up to 30 kilograms). The selected mesh widths, thread sizes and weaving patterns determine the strength.
One of the very first plastic net packaging for onions
Recyclable material and water-based inks
Onion net packaging is made from mono-material polypropylene. The production process of polypropylene (PP) is environmentally friendly and is guided by the principles of the circular economy. Film is extruded from granulate. This is cut into wide strips from which - just like with textiles - threads are produced with which the coarse-meshed net material is woven. By using different thread sizes, different strengths are possible. The production of PP uses much less energy, water and raw materials than with paper, which results in a low ecological footprint. Both the header band, the laminated brand print and the woven material are fully recyclable. Only water-based inks are used for the printing. (source: the Royal NNZ Group).
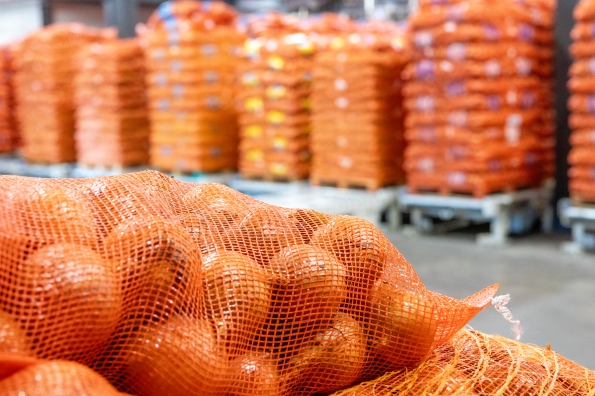